3Dプリンターを使って積層面で可動するヒンジを一体形成しよう 他のオブジェクトをサポートとして利用できます
実はたいした種も仕掛けもなく、がっかりさせたら申し訳ありませんが、サポートレスで普通のヒンジを作れないかな・・・?と思い試行錯誤した結果です。3Dプリンターでヒンジのような動くジョイントを作る方法はいろいろありますが、よくある一般的なヒンジを一体形成できるか試してみたところ非常にうまい具合に動かせたのでご紹介させていただきます。
一体形成のヒンジを作ろう
今作っている便利グッズでヒンジが必要になりました。作成したいのは、そこそこ大きめなヒンジで、1kg程度のものが支えられる程度のものです。皆さんヒンジってどうやって作られていますか?王道としてはヒンジを構成する部品をつがいで作って、間にネジとボルトを通す方法でしょうか・・・?
金属製が一番安定感があるのは確かですが、そこまで強度は必要なくて、3Dプリンターのみでヒンジ作れないかな、というのが始まりです。せっかく3Dプリンターがあるわけですし、組み立て不要ですぐに使える安定した一体形成のヒンジが作りたいですよね。また、サポートなど材料も無駄にならないのがベストです。ちょっと調べてみると、やはりヒンジを作りたい方は多いようで、寝かせて作るヒンジの作成について書かれたページが多い印象を受けました。
ということで今回は右のようなヒンジを一体形成する手順について忘備録もかねて共有させていただきます。とはいうものの全然大したことはなくて、設計と積層、材料の反りをちょっと利用しただけです。使用プリンターはsnapmaker2.0ですが、FDM機どれでも出来るはずです。
3Dプリンターで作りやすいヒンジについて
まず前提として、寝かせて作るすり鉢状?ヒンジは重力に逆らえない積層型の3Dプリンターを前提とした一体型ヒンジの最適解です。ヒンジはすり鉢状の形状として凸部分が、接する凹部分に寄り添うように造形していることが多いです。(下図参照)こうすることで無理なく横の形状にハマり込んだ形状に出来ます。公開されている様々なモデルでも採用されていて実績があり、造形難易度も低いので私もよく利用していました。
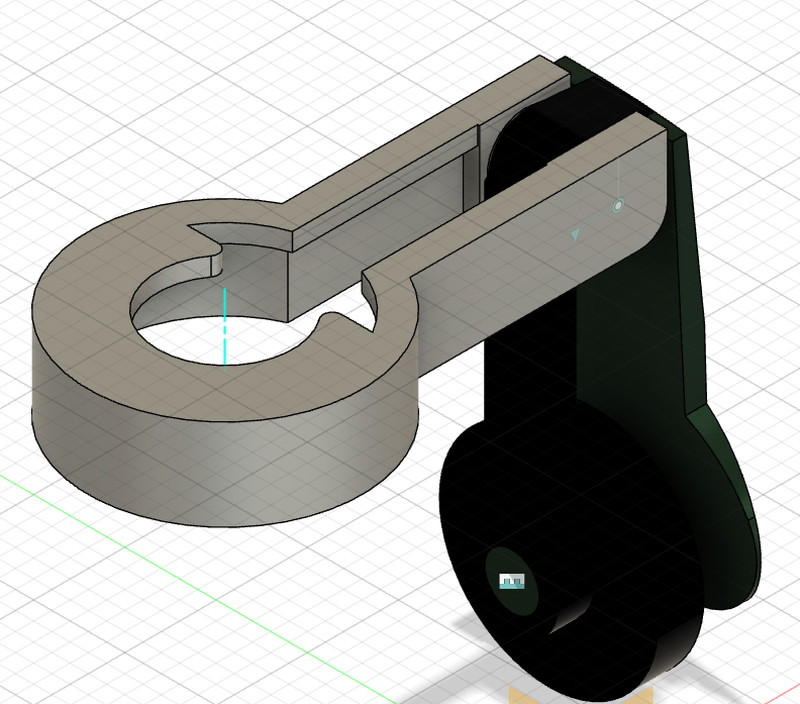
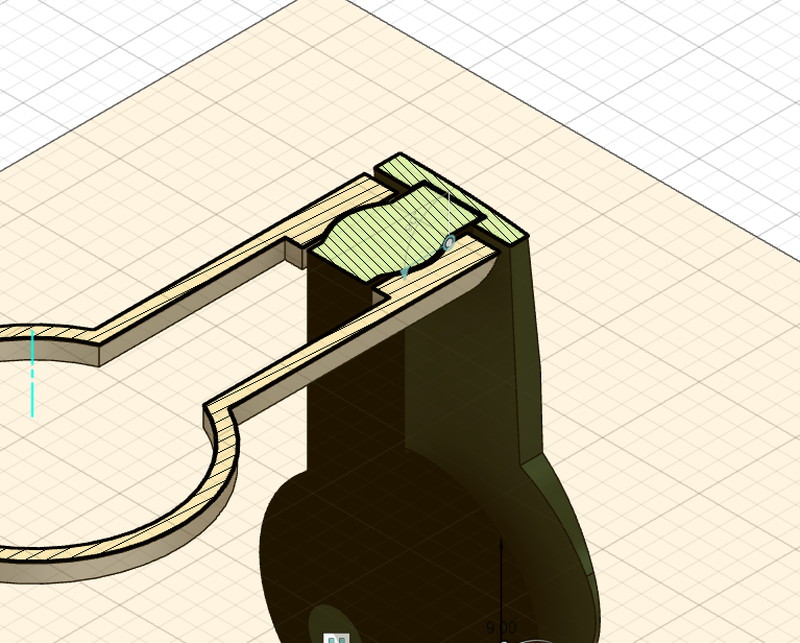
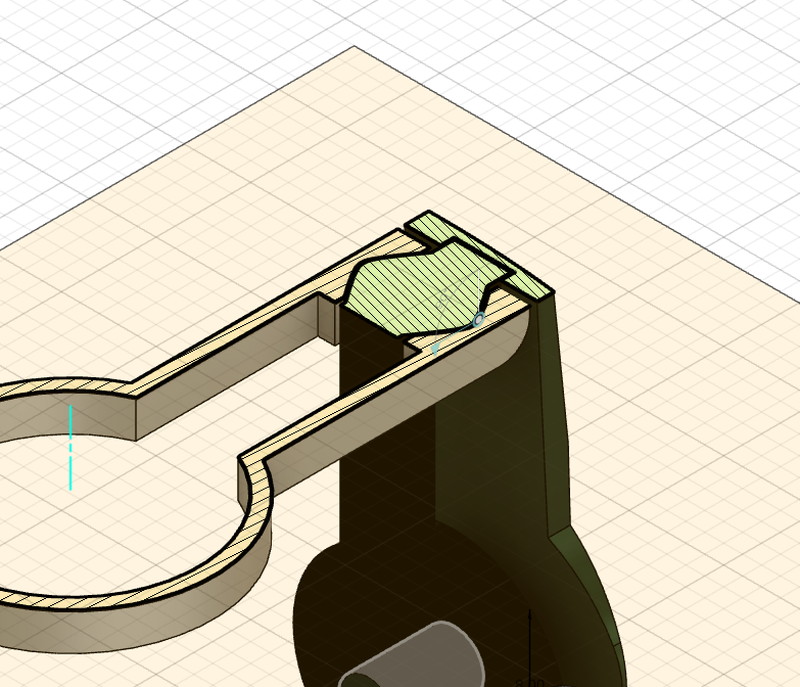
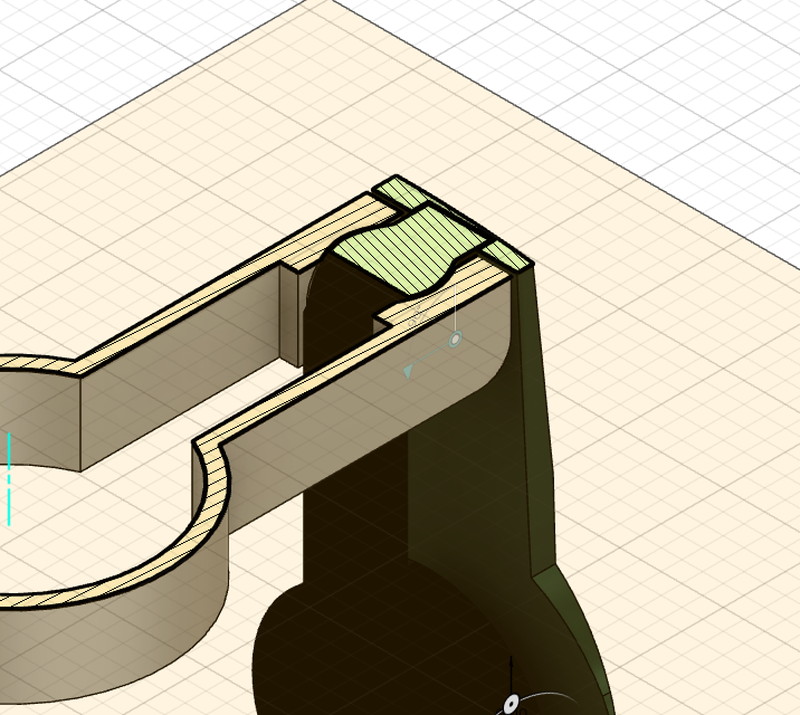
個人的に思うこの方式の欠点はあそびが大きいところ、荷重がかかった際の形状同士の接触面が小さいところです。すり鉢形状下面に荷重が全て掛かるため、部品中央が歪みやすいと思うんですよね。また、一定以上の摩耗でもヒンジが脱落する可能性があります。また、ヒンジを横方向に寝かせなければならないため、形状によってはヒンジ以外の部分にサポートが必要になります。
一方でブリッジを利用して浮かせて動く造形物を作る手法も多いと思います。Thingiverseにも多くの作例があり、上下部分を工夫しつつ数センチ以内のブリッジで可動部を製作する手法です。この方法も自由度が高いのですが、ブリッジ方向は重力に対してほぼ直行しなければなりません。遊びが大きいのが特徴なのである程度上下左右に動かしたい場合に向いています。
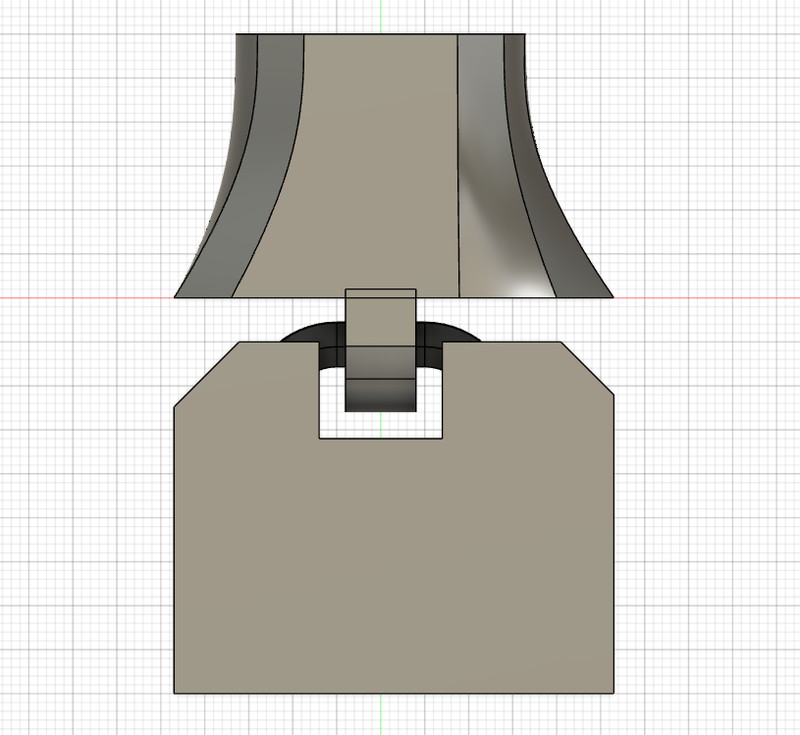
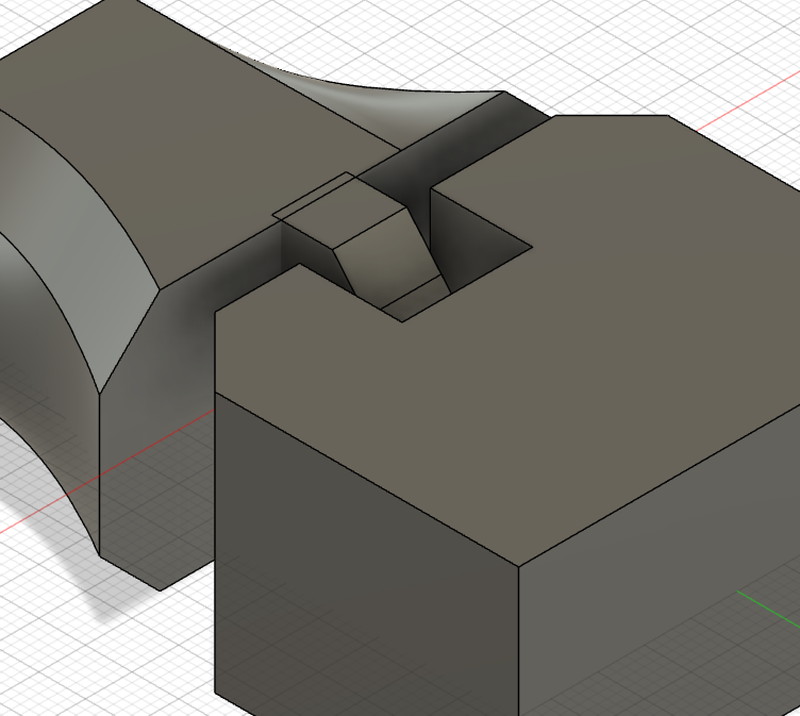
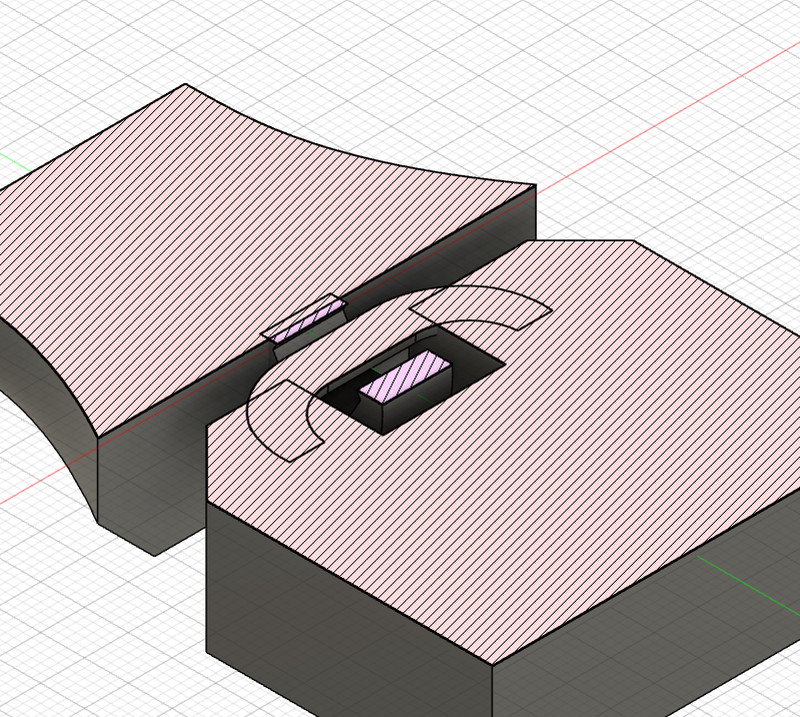
よくあるヒンジ(蝶番)を3Dプリンターで作れるか?
今回作りたいのはどちらかというと拘束性が高く、1方向のみに動く一般的な蝶番です。私たちが一番よく目にする下図のようなヒンジは、構造が単純で遊びが少なく、大きさが変更しやすいのが利点です。また、回転中心の棒部分でぶら下がるものが棒と接する範囲が広いため、荷重が分散されると思うんですよね。
ただ、ご存知の通り棒を3Dプリンターで作ると積層方向で割れやすいです。特に細いとねじれにも弱くて、「3Dプリンターでネジは作るな」と言われる所以にもなっています。確かに所謂「抜き差し蝶番(下図)」を2つの部品で作った場合を考えると、支える軸の根本で折れそう・・・。
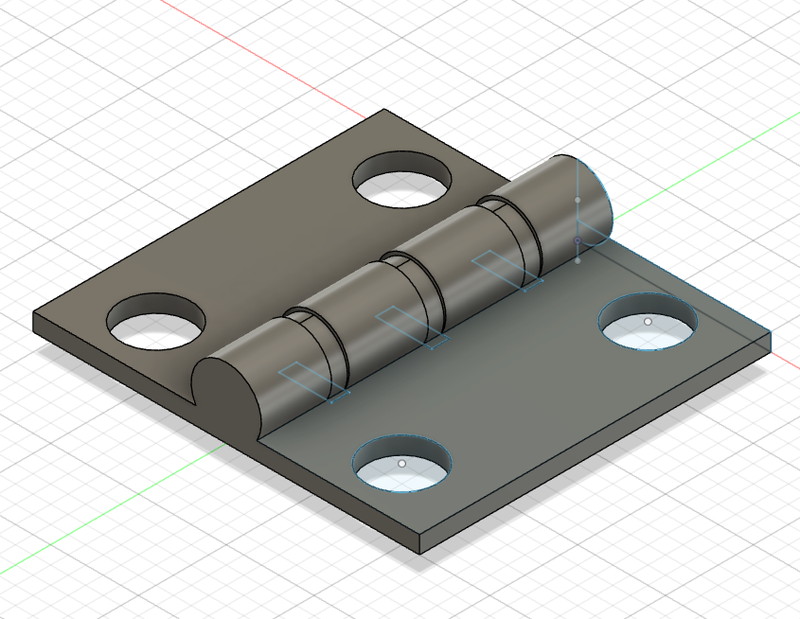
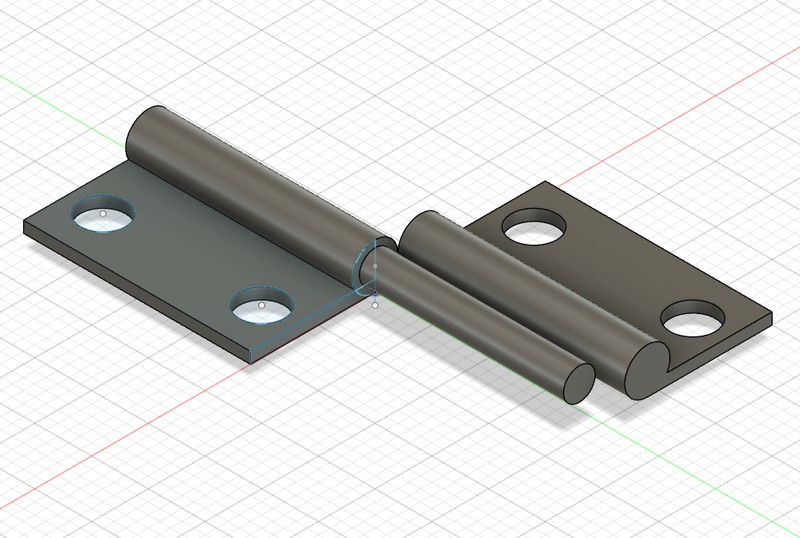
ただ、1点に力がかかった場合や捻れには弱いものの、両側に支えの形状があり、かつ複数の蝶番面に荷重が分散されれば積層で破断するリスクはかなり減るはずです。この「よくあるヒンジ」を縦置きして作れれば積層と並行なので摺動も安定しますし、摩耗に強く、立てて造形できるので私の欲しい部品にぴったりです。でも実現にあたっては大きな課題があります。ご存じの通り、積層です。普通の蝶番を作ろうとすると、重力に平行な面が生まれるためサポートが必要になります。ヒンジの内部にはサポートを入れられませんし、組み立て型のヒンジであれば作成可能ですが、材料も時間も無駄が多くなり組み立てる工程も面倒です。
従来型ヒンジの設計 下面をサポートとして利用する
単純な設計で捻りもなくてがっかりさせたら本当にすいません。設計と造形は「ヒンジ部分を可能な範囲で同一形状として、下のオブジェクトに上のオブジェクトの支えになってもらう」だけです。サポートがぽろっとはがれるように造形すれば問題が解決するというわけです。
ということで、設計時はヒンジの上面と下面に隙間が必要です。0.4mmノズル、一般的なPLAでの設定になりますが、この隙間は0.4mmにします。0.2mmの一般的なサポートの隙間だとくっついて離れません。0.4mmはすっとはがれて造形が破綻しない最小間隔になります。0.3だと造形時面倒になります(後述)。また、上面と下面で形が異なるとサポートにならないのでヒンジパーツは同一スケッチから作成するのが良いと思います。
さて、単純ですが設計の説明です。全部を半分で作ってミラーしてもよいのですが全体がつかみにくくなるので最初から全体を作っています。まずスケッチは下図のようにしています。あまり小さいサイズだと作りにくいですし強度も心配なのでこの数値にしていますが、自由度は高いのではないかと思います。まずはヒンジパーツを2つ作ります。なお押し出し量(造形時の高さに相当)はスライス厚0.2mmの整数倍になるようにしてください。
ねじホールがついたほう(パーツ1)は普通に押し出して作成し、もう片方(パーツ2)は同じスケッチからオフセットして作りました。必要なヒンジ数にしたうえでブーリアンでくりぬきます。元の形状も残せばとりあえずヒンジ完成。パーツ2の板形状も押し出せば大枠は完成です。
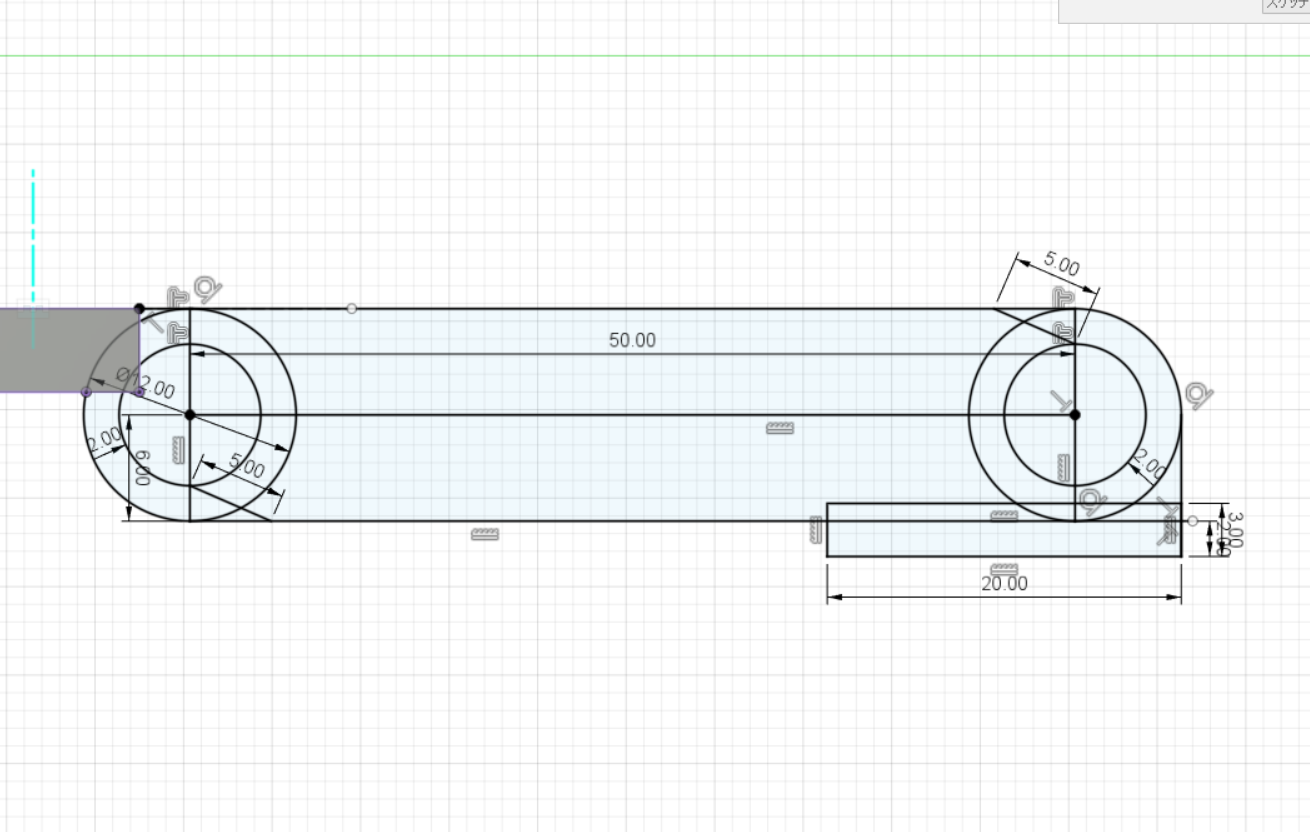
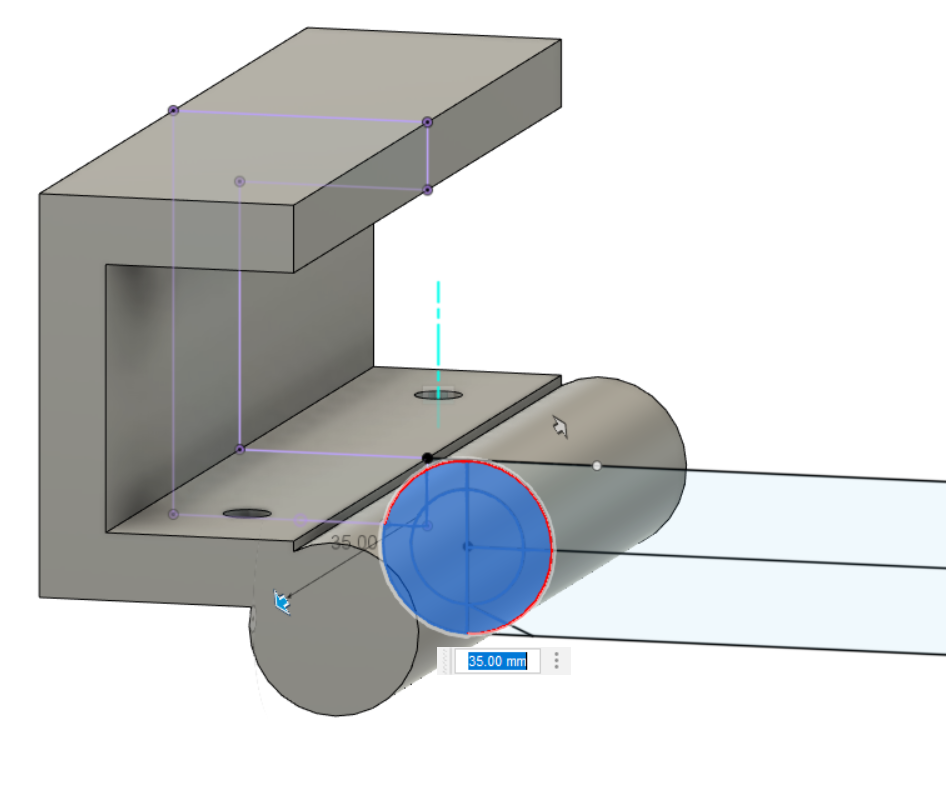
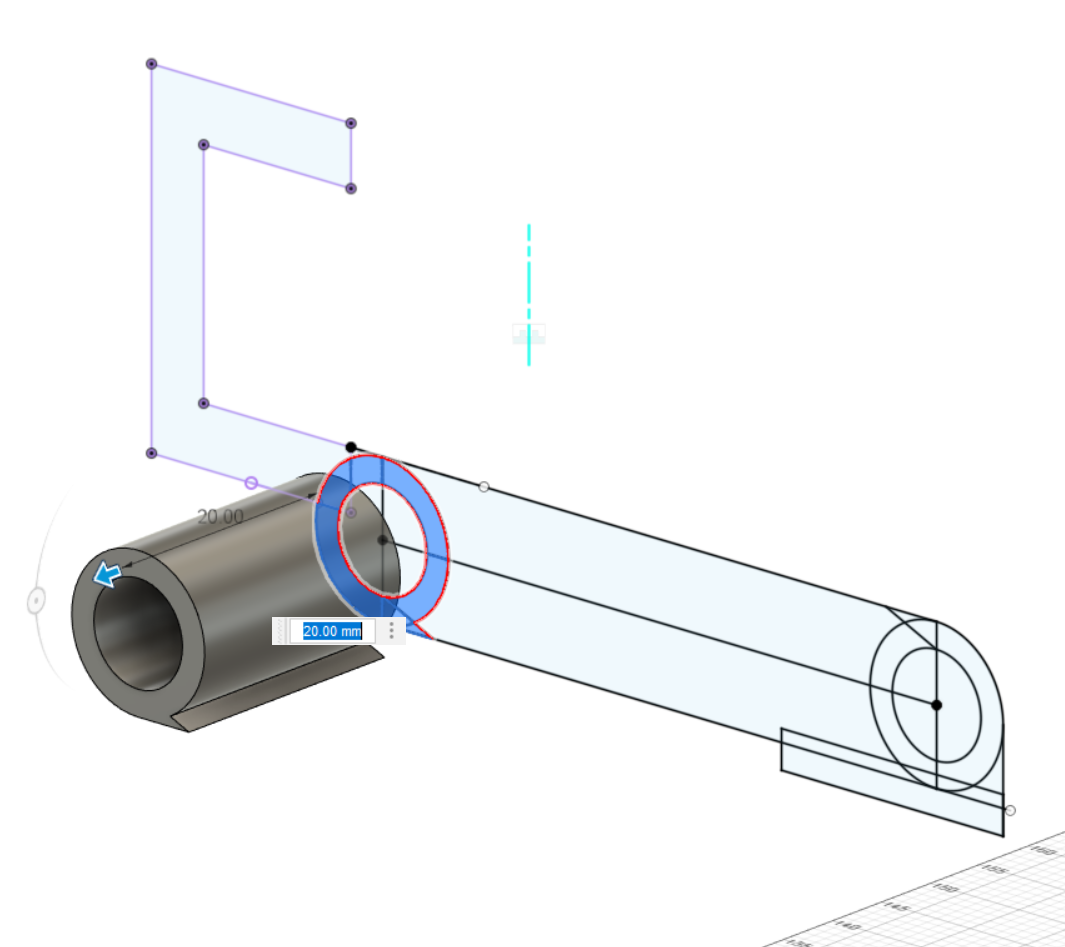
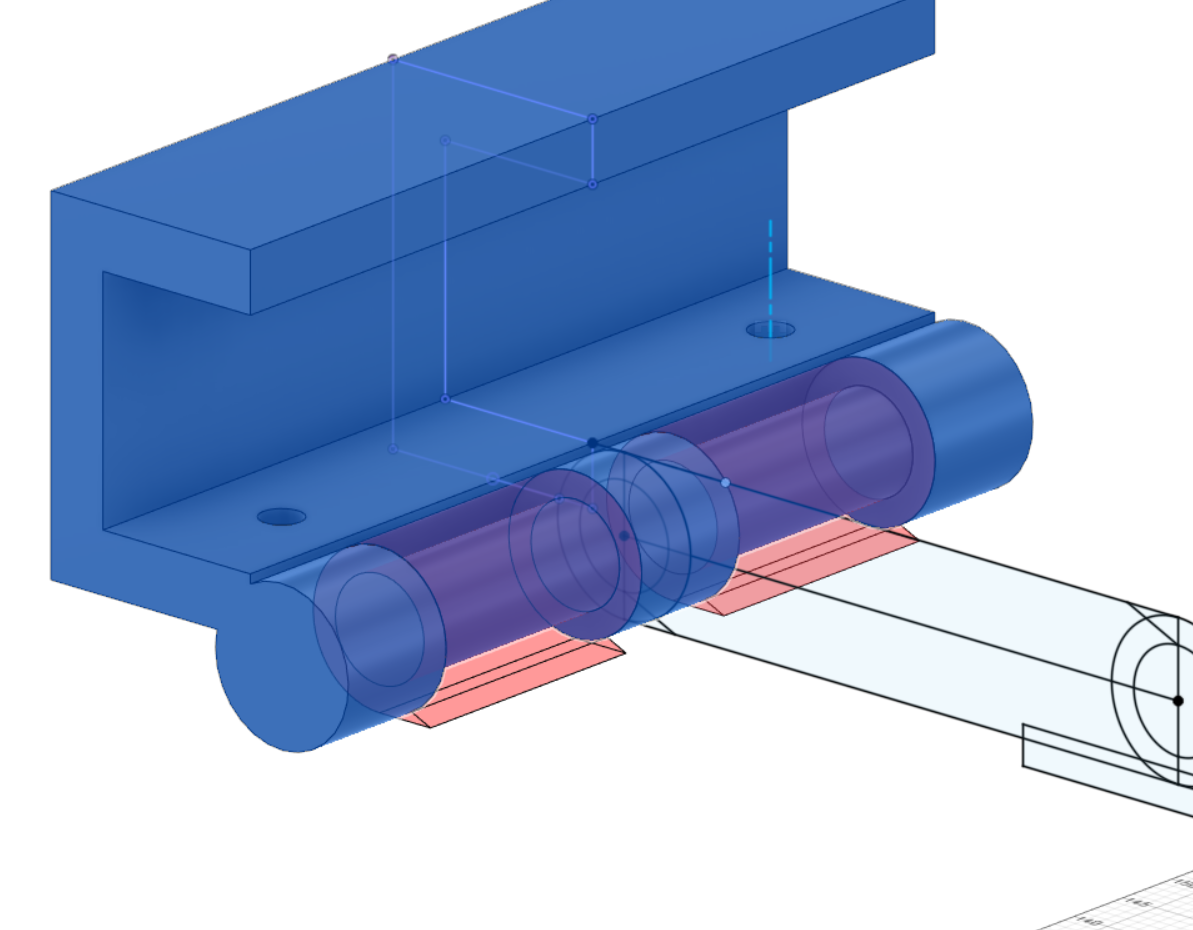
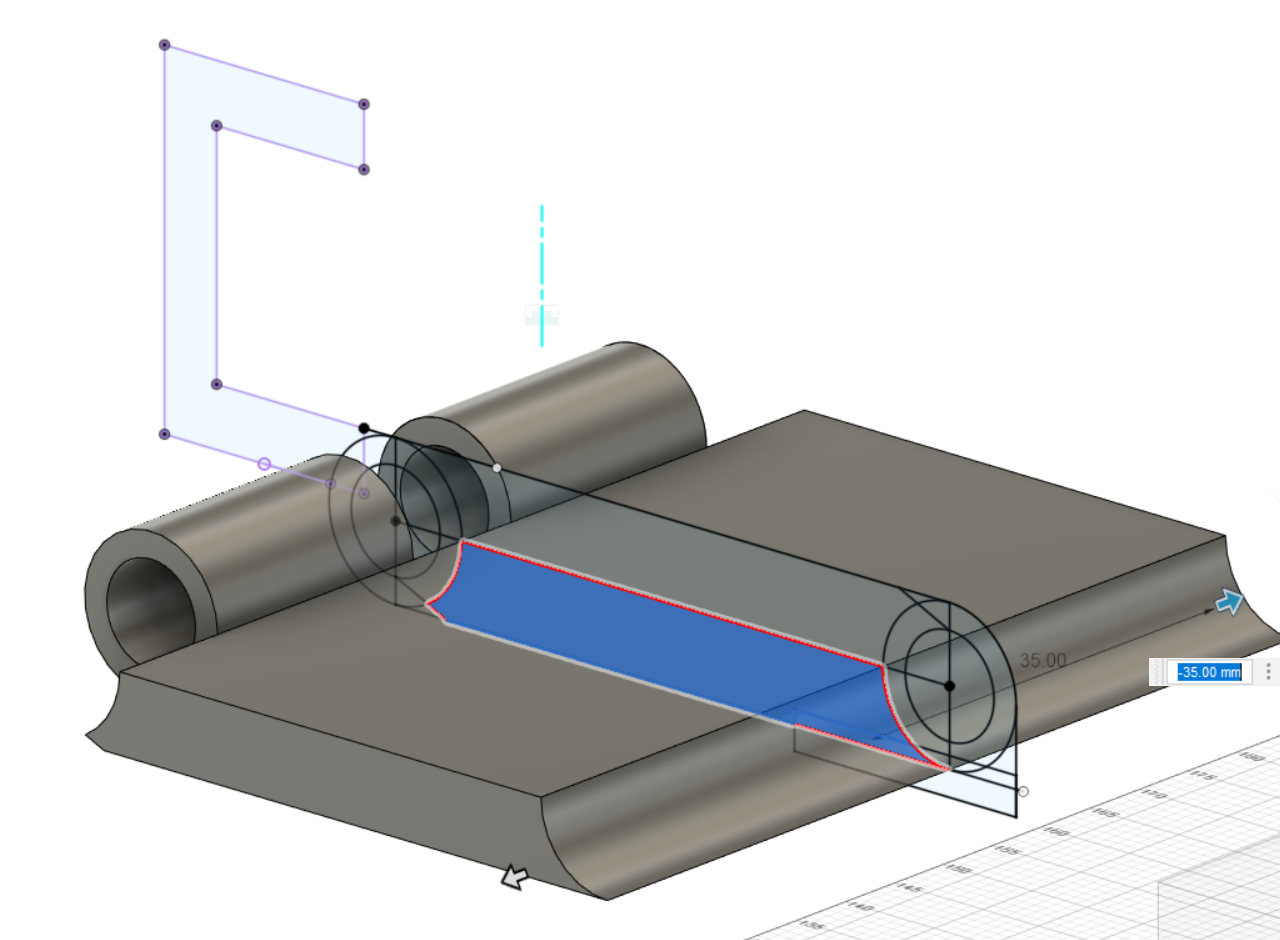
この状態だと隙間がないのでオフセットで隙間を作ります。プリンターにもよるとは思いますが、先程の通りパーツ1側のヒンジ接触面は-0.4mmにしてください。芯は中でシームが必ず発生するのであまりぎりぎりだと中でくっついて動かない塊ができます。ぐらつきも少なくいい塩梅だったのが今回の我が家では-0.8mmでした。パーツ2のほうは-0.3mmと0.1mmずらしてあります。少しずれたほうが上下でパスが少し変わってくっつきにくくなる気がします。(気のせいかもしれない・・・)図ではもう一軸作った際に隙間ができるようにパーツ2乗面もオフセットをかけています。
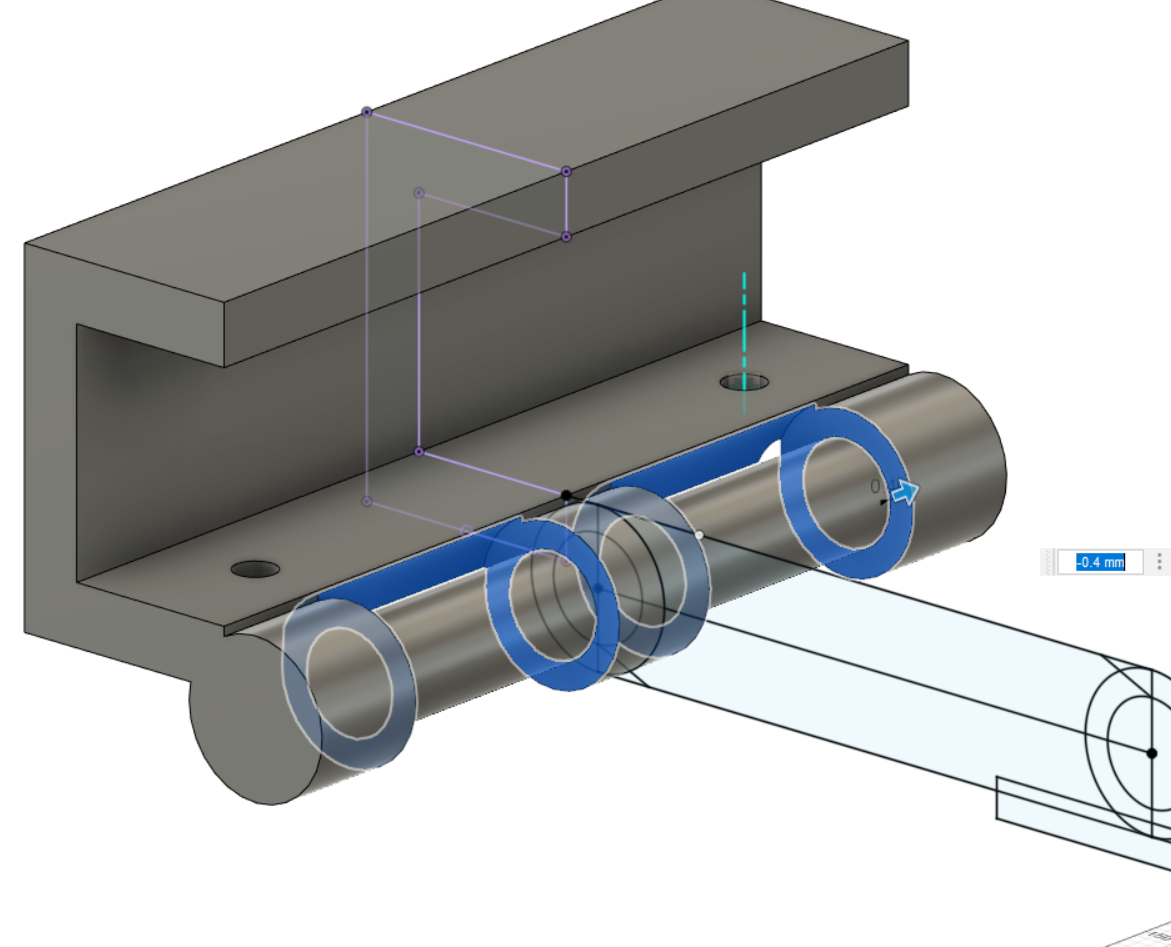
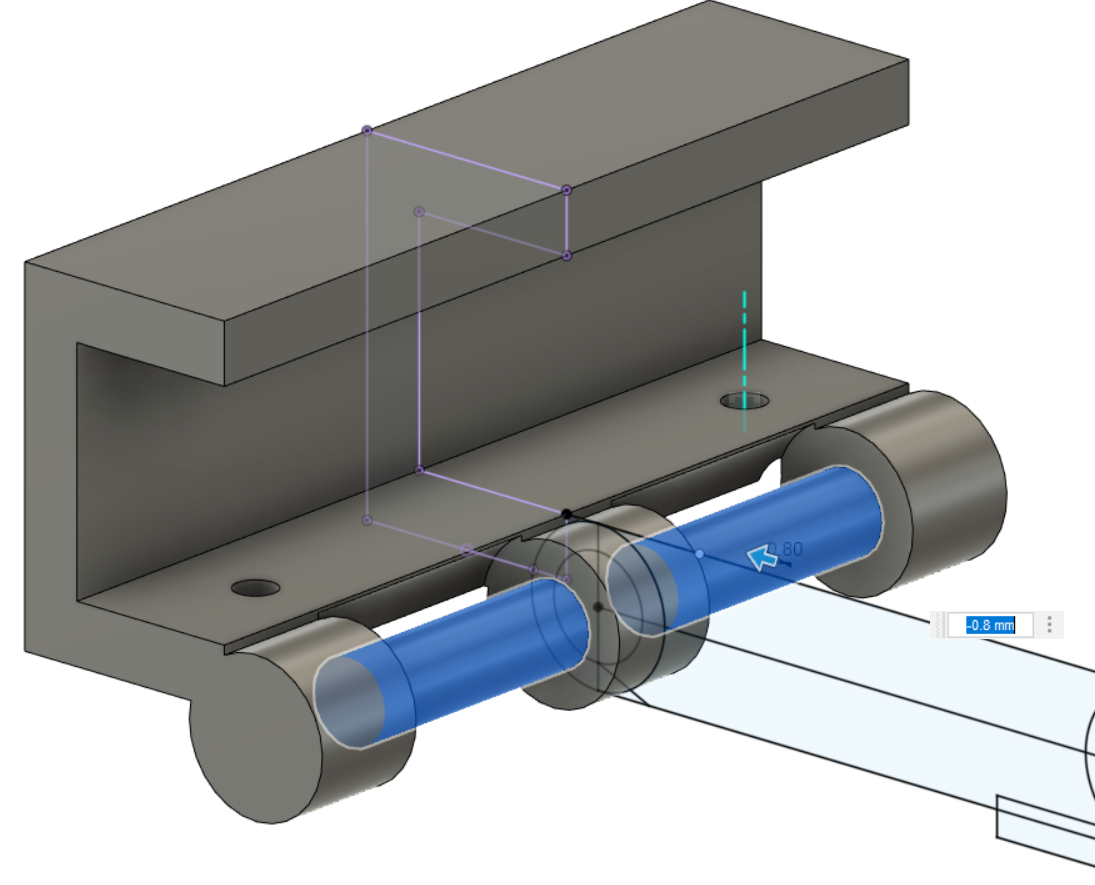
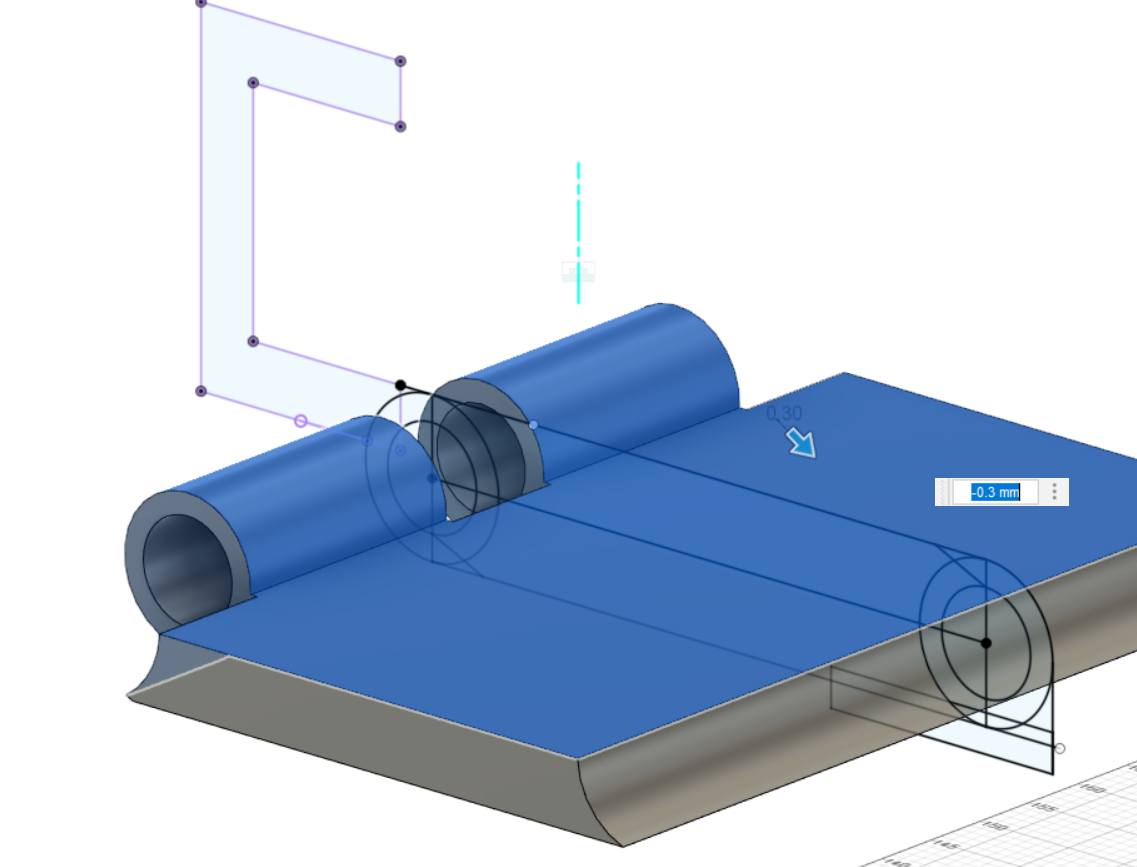
出来上がりが下図になります。
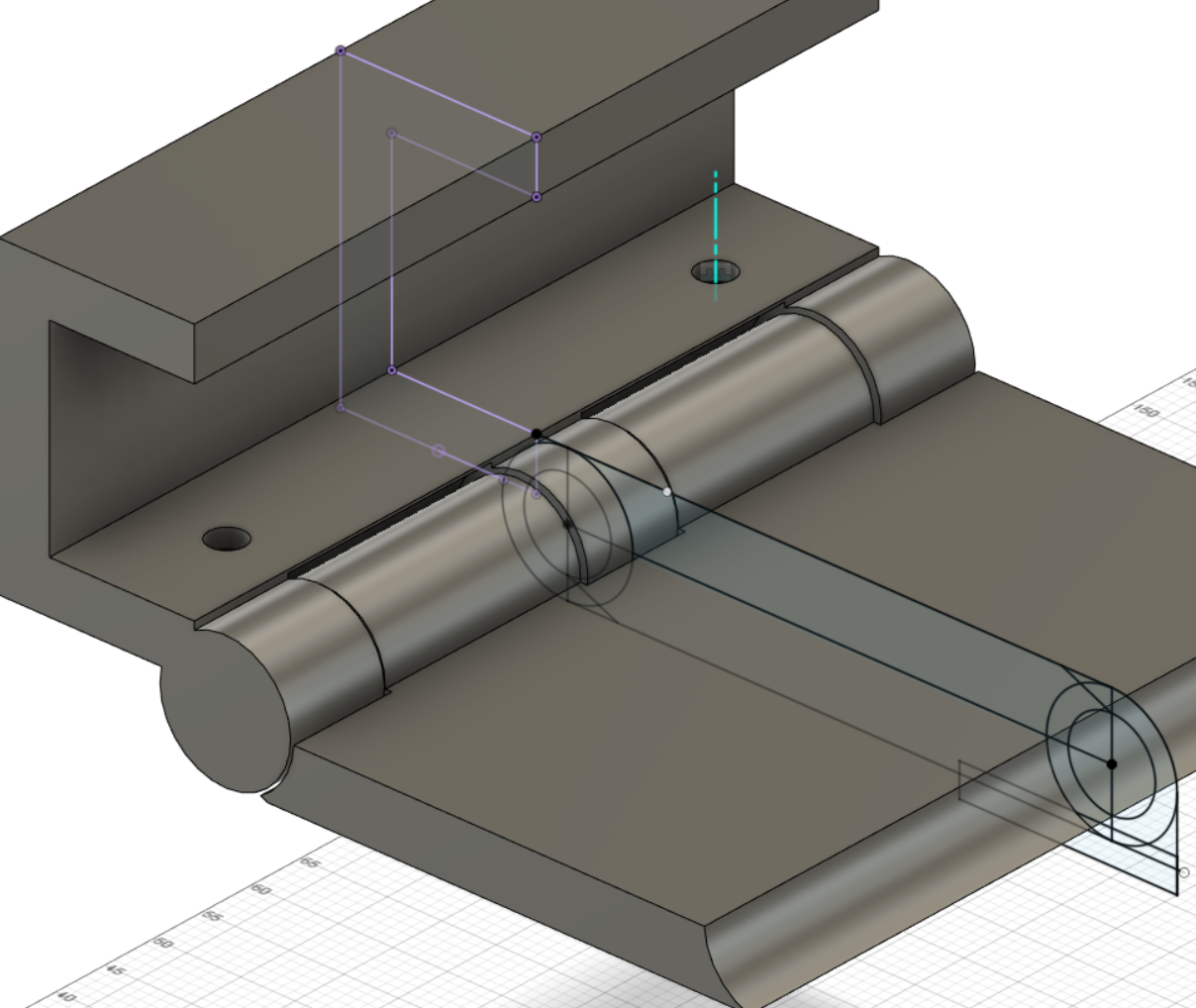
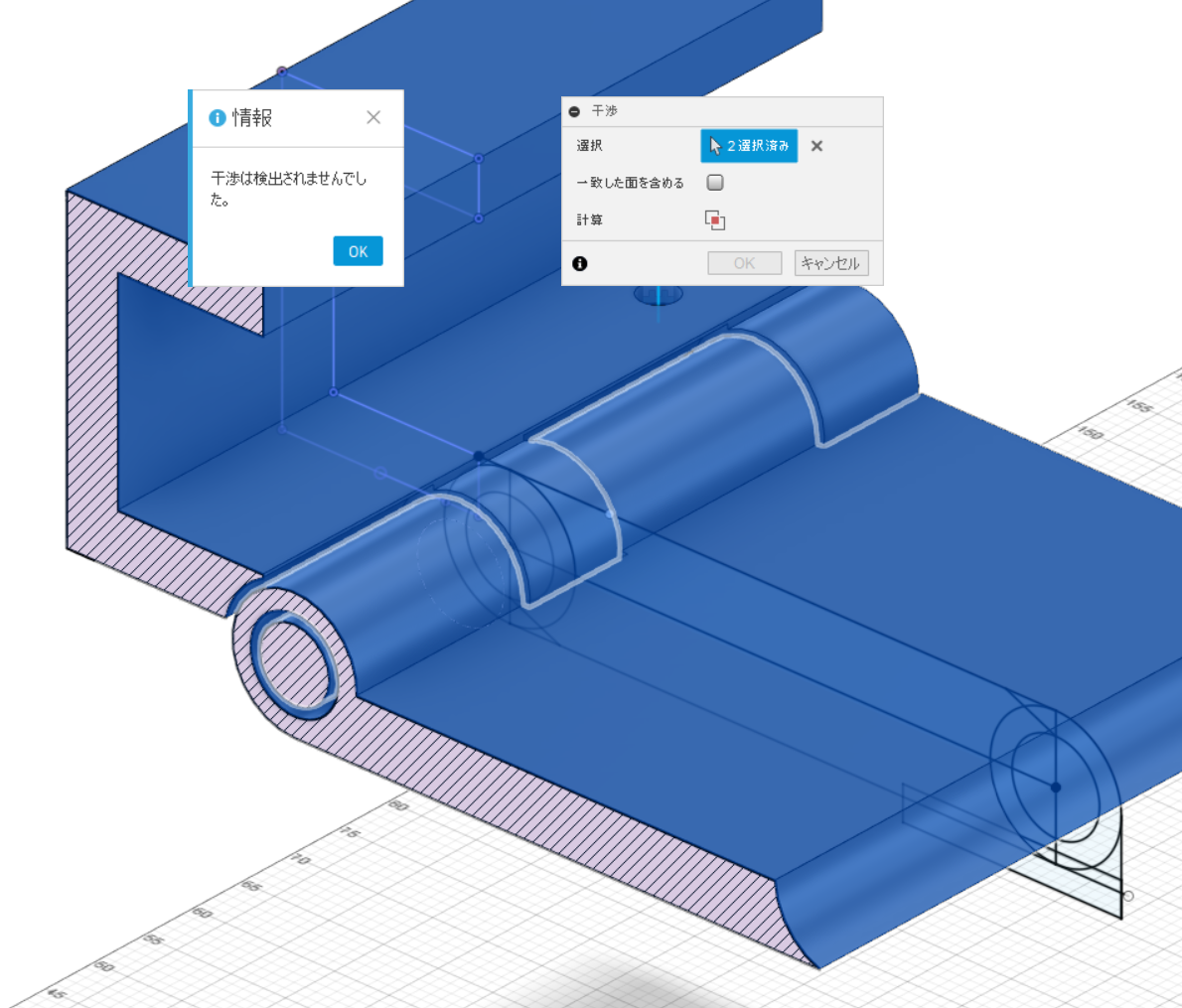
私が欲しかったパーツはもう一段ヒンジがついたものだったので同様の手順で作ります。必要があればジョイントにして角度を変えてもいいと思います。どの角度でも造形には影響しませんので折り曲げながら並べて、ジョイントを複数作って長いものも作れるはず。下の図が出来上がりです。これをこのまま立てて造形します。
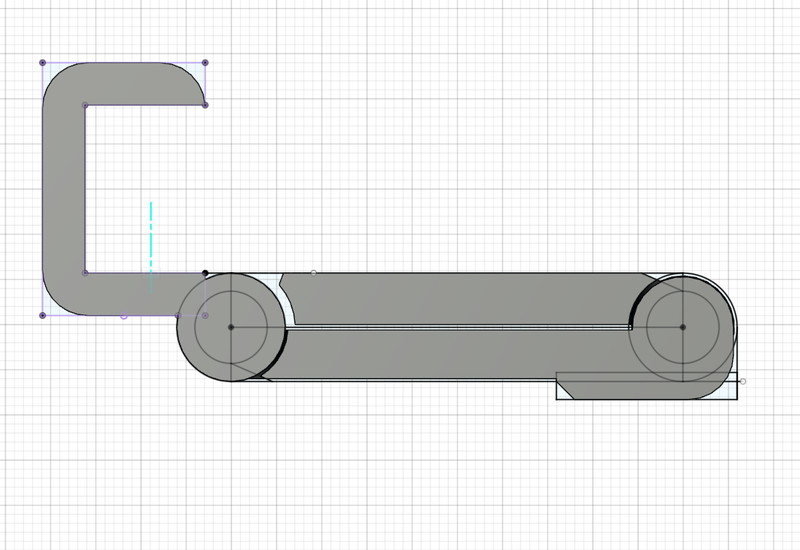
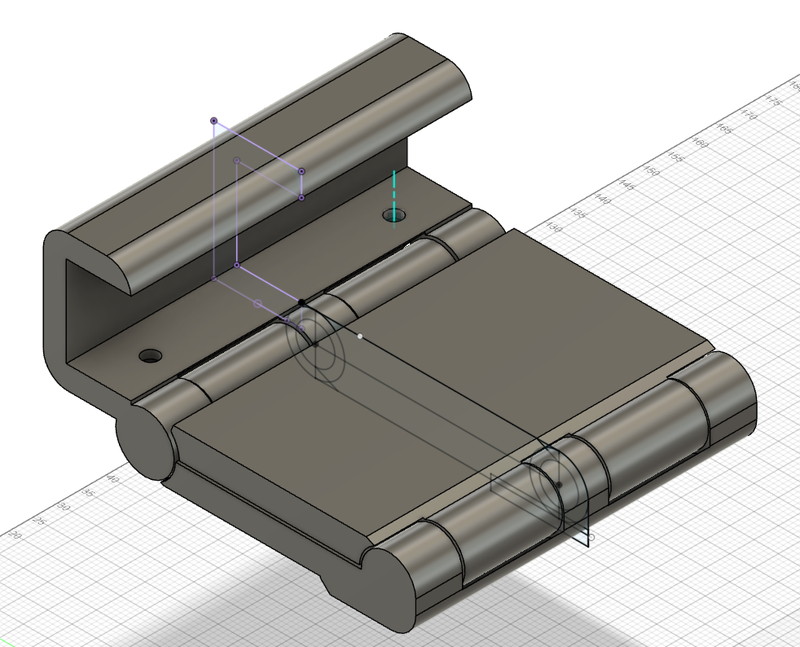
上のヒンジのSTEPファイル(Wordpressの都合上、zipになっています)もよかったら参考にどうぞ
造形設定
造形はPrusaSlicerで行いました。Curaでどうなるかは試していません。造形設定の肝は
- 積層厚は1層目もそれ以降も0.2mm固定とする
- あまり造形スピードを上げすぎない(内壁60mm/s程度、外壁はより遅く)
- ファンは100%にしておく
- 吐出量は必要以上に増やさない
です。これで設計時の高さやヒンジ開始位置は層と一致しますので2層分開けて上の部品が造形されます。隙間が多い分フィラメントがだれるので、造形速度は早すぎるとパスが短絡しすぎてしまいます。ファンはしっかり回すことで下層とくっつかないようにできますし、さらに造形が進む際にフィラメントが少し反って、積層方向のヒンジ部分の隙間が空くように変形します。これによって適切なクリアランスが確保されます。
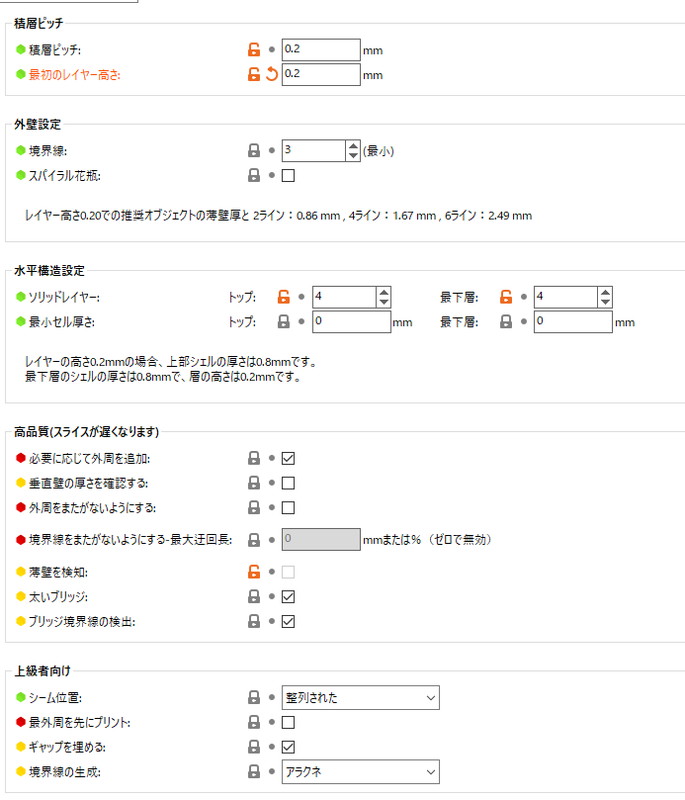
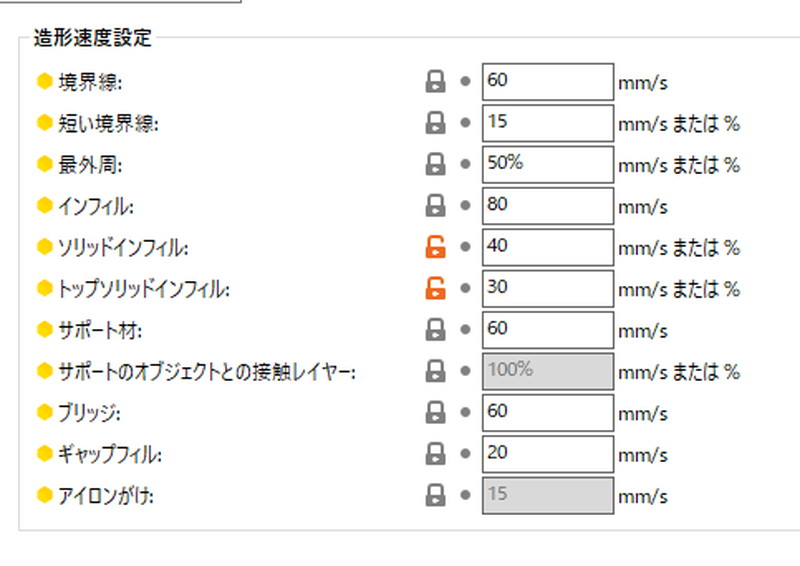
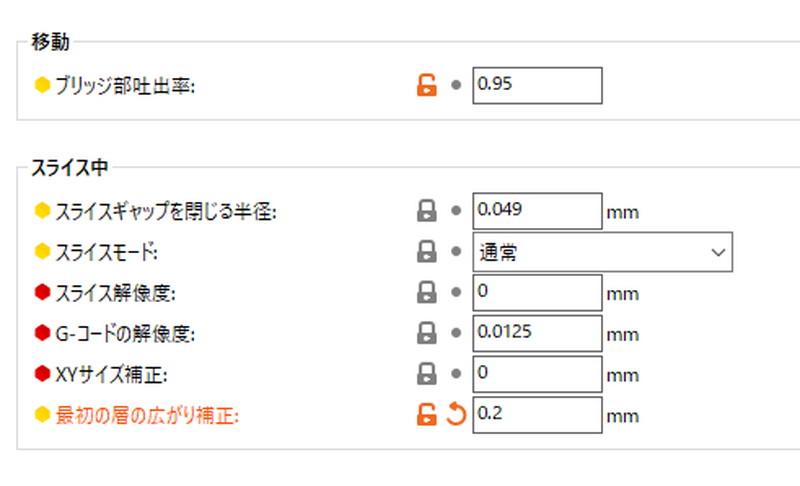
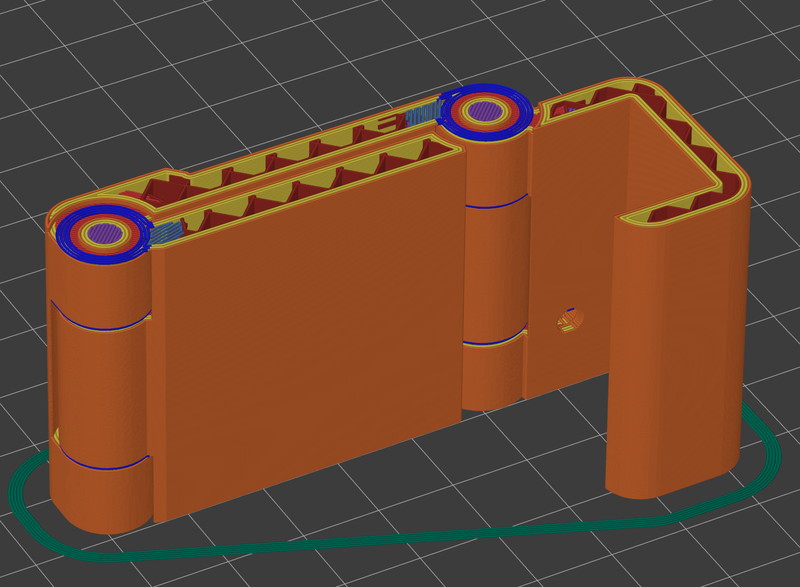
これを出力したものが下になります。各ヒンジがちゃんと可動し、積層方向と可動方向が平行なので非常に動きは良いです。また、サポートもなく余計なことをしないので材料も無駄になりません。形状が違う試作中の断面の写真もありますが、内部のクリアランスも相応に確保されています。動きも問題ありません。
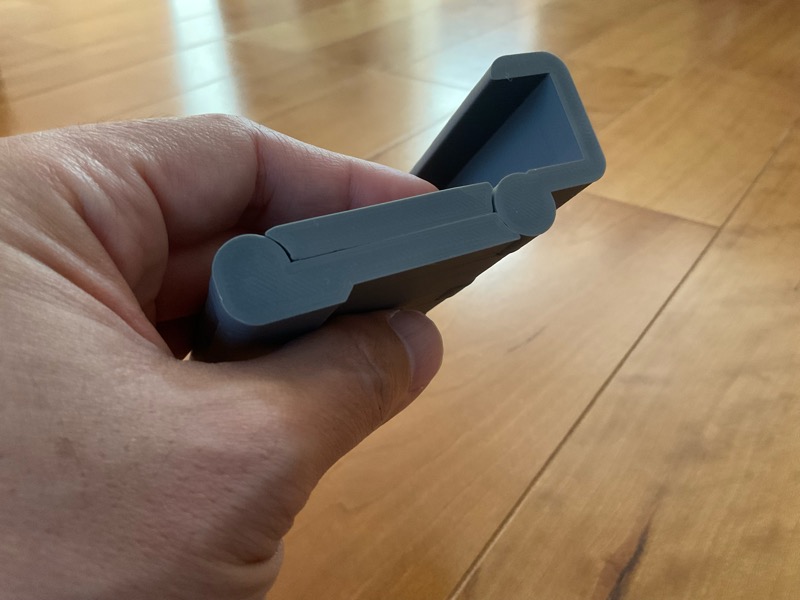
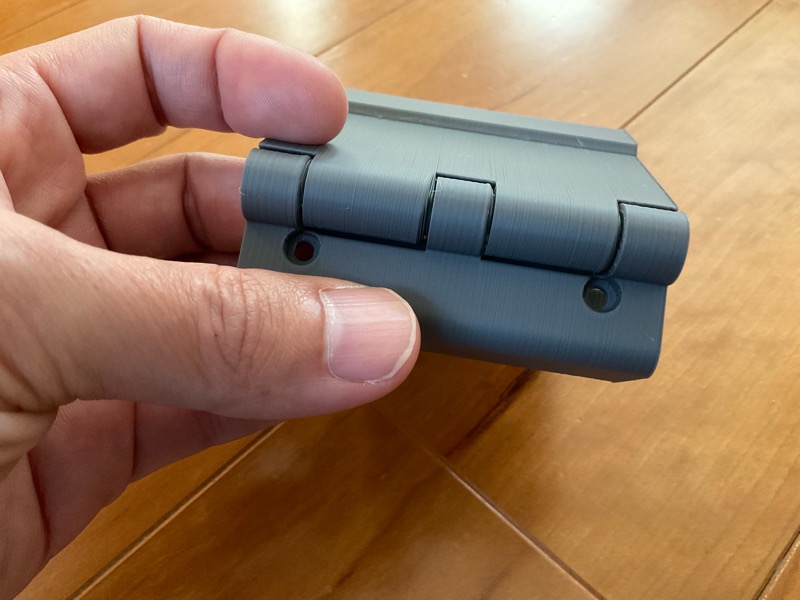
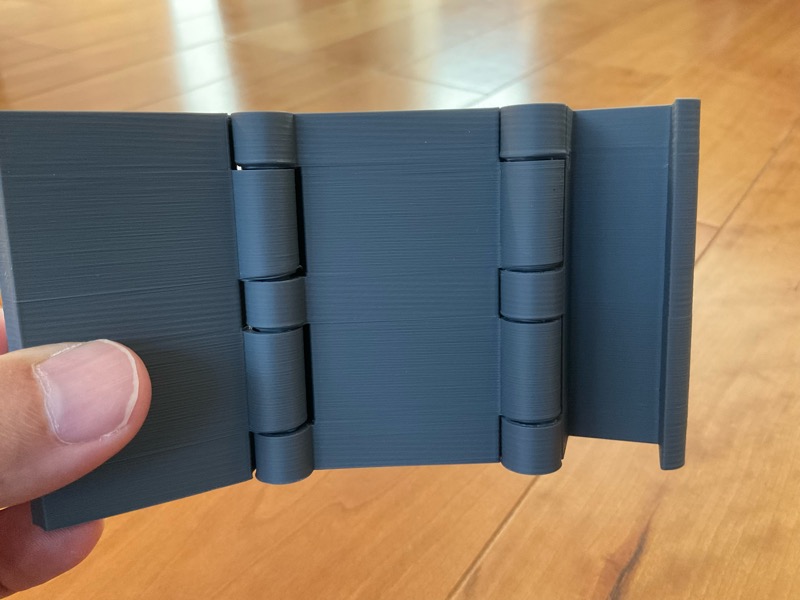
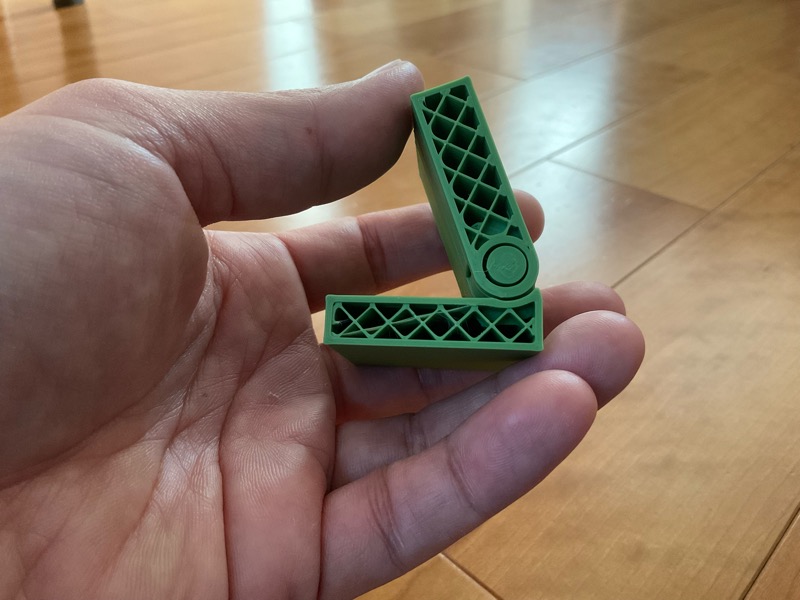
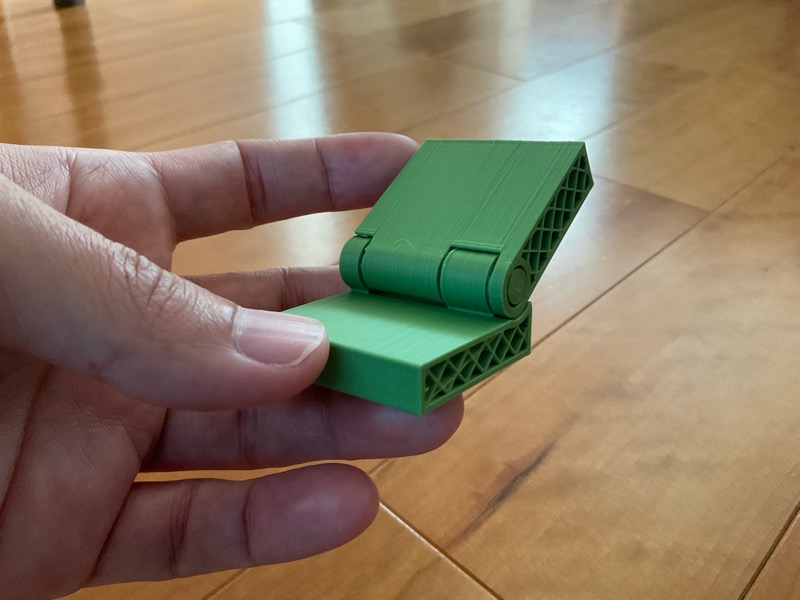
ヒンジ数を増やせば負荷にも対応できそう
さて、うまくヒンジ動きましたでしょうか?この方式であれば支柱の両端にせん断力がほぼ均等にかかるので、ヒンジの数と間隔次第で様々な負荷に耐えられそうな印象です。また、造形時のヒンジ角度に制限がないため、ビルドプレート内に複数の部品を配置したり、履帯のようにつながった帯状の部品を作るのも出来そうですね。TPUで以前作成したベルト状のものが作れるのは夢があります。
試していませんが、小径ノズルで同じ手法が使えれば、比較的小さなヒンジも作れるかも?という期待もありますし皆さんぜひ試してみてください。また結果を教えていただければ幸いです。
今回も最後までお読みいただきありがとうございました!
ディスカッション
コメント一覧
まだ、コメントがありません