オーバーハングを克服しよう 3Dプリントを前提としたモデリングやスライスのコツ Prusaslicer 2.6 は魅力的
3Dプリンターが層ごとに造形する以上、避けて通れないのがオーバーハングをどうするか、という問題です。先人の方々が色々な対策を打ち出しておられるのは皆さんご承知の通りですが、せっかくなので当方の工夫についてまとめました。スライサーも進化しており、Prusaslicer 2.6にはDynamic overhang speed や Extra perimeters on overhangsといった機能が追加されましたのでこちらも紹介させていただきます。
オーバーハングって?その問題点について
ご存じとは思いますが、初めての方もいらっしゃるかもしれないので・・・。
FDM方式の3Dプリンターは下から順に樹脂を積み上げていくため、底面積より上が大きくなるシーンが多々あります。ここをオーバーハングと呼んでおり、その角度が一般にその角度が45度を下回ると造形がしにくくなってきます。
また、何もない空間にいきなり樹脂を置くことはできないので、オーバーハングの問題はこの「空中にどうやって樹脂を積み上げるか」と直結しています。ある程度は3Dプリンターの条件で(マシンや樹脂の特性)解決し、それ以上はオーバーハング部分を含め、必要に応じてサポートと呼ばれる構造材を積み上げて置き、その上に必要な樹脂を乗せる作業を行っています。
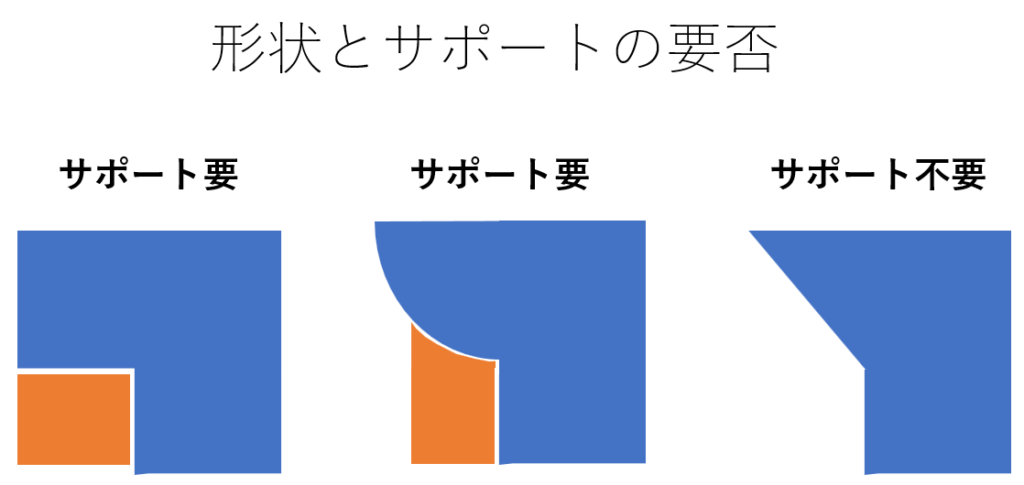
簡単に取れる部分のサポートであればサポートを積み上げて解決すればよいのですが、内部等サポートが取れない部分をどうするかも問題になります。よく言われる「オーバーハングに強い」「オーバーハングに弱い」というのはサポートがない状態でどの程度造形が正確にできるかを示しており、十分な冷却が出来ていれば30度くらいのオーバーハングは問題なく造形できますが、寸法安定性は厳しくなります。
オーバーハングの問題は造形プロセスにも関わっており、オーバーハングの端っこで樹脂が盛り上がったり反った場合、そこにノズルが衝突し造形物が破壊されたり、ベッドから剥離してしまったり等の問題が生じえます。また、支える天井部分の樹脂が崩壊することでその上の造形も不可能になるなど問題を生じます。
モデリングの工夫 スライスを意識したモデリング
オーバーハングの克服なのにこんなことを言うのは憚られますが、一番の解決方法は厳しいオーバーハングを減らすモデリングです。工夫の基本は下記の通りです。
- 造形方向を意識してオーバーハングが少なくなるよう面取りする
- 天井はブリッジできるように平らにする
- 無理なところはサポート前提で、平面を多くする
オーバーハングになる部分はフィレットを使わず面取りをしたり、モデリングする時点で造形方向を意識してオーバーハングを少なくしましょう。特にフェレットは滑らかな曲面は魅力ですが、オーバーハングとして考えると相当に厳しいです。
オーバーハングがきついところは逆に平たくしてしまったほうがサポートがつけやすかったり、ブリッジと言って樹脂を橋渡しして解決するほうが造形は楽になります。穴は6角形にしたり、円や球の天井は平たくする、といった工夫も大切です。この手法は多くの方が実践されているのでぜひやってみてください。
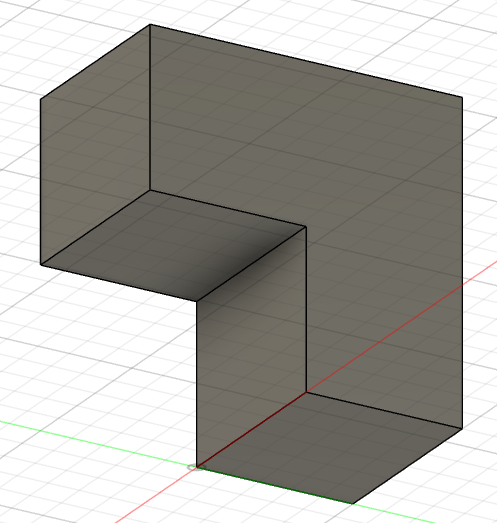
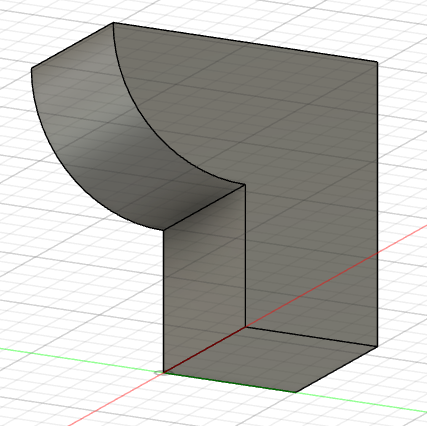
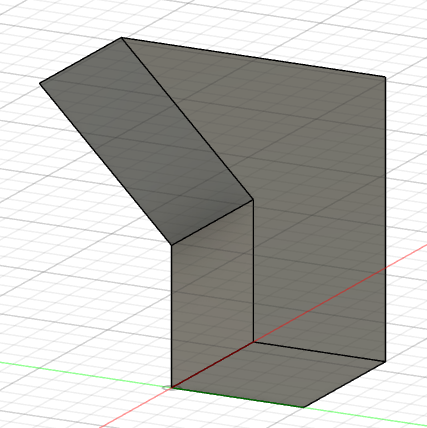
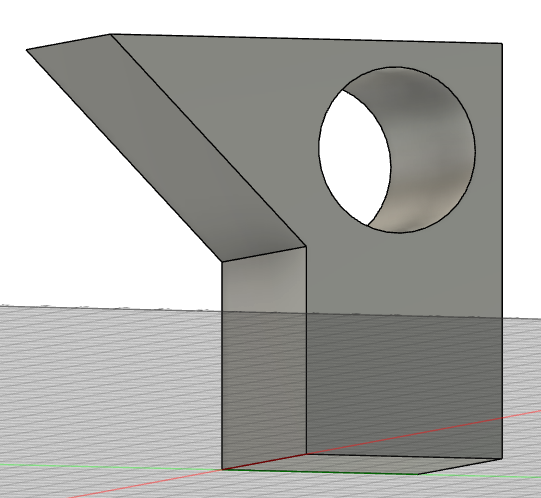
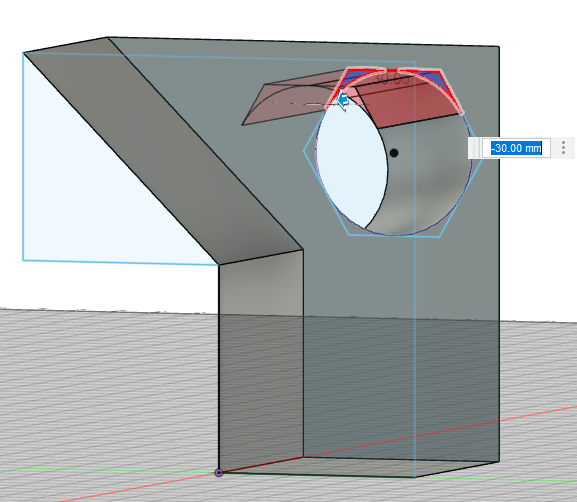
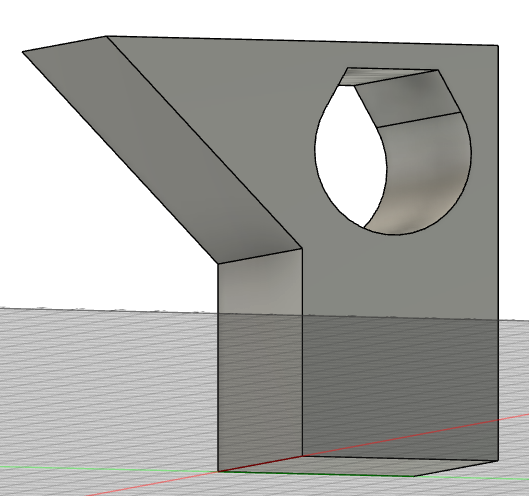
ではサポートレスのオーバーハングで難しいものの一つ、球面形状がなるべく必要な時はどうでしょうか?単純な平面にできない場合、曲面を閉じるところでオーバーハングが限りなく0度に近づいてしまいます。
そんな折、先日自分が思いついた解決方法が下記です。オーバーハングが厳しくなるところを7角形にして中点ごとに適宜形状を作成します。最後元の形状からくりぬくことで球の内面を直線で結ぶことが出来、パスが宙に浮くことを防げます。
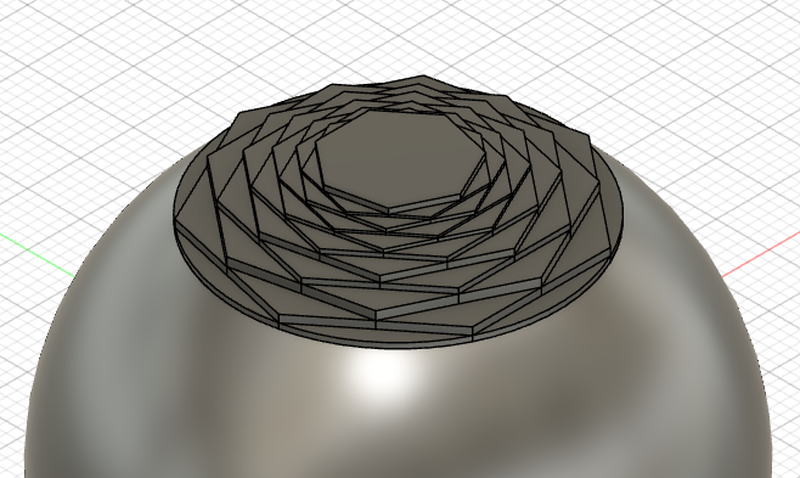
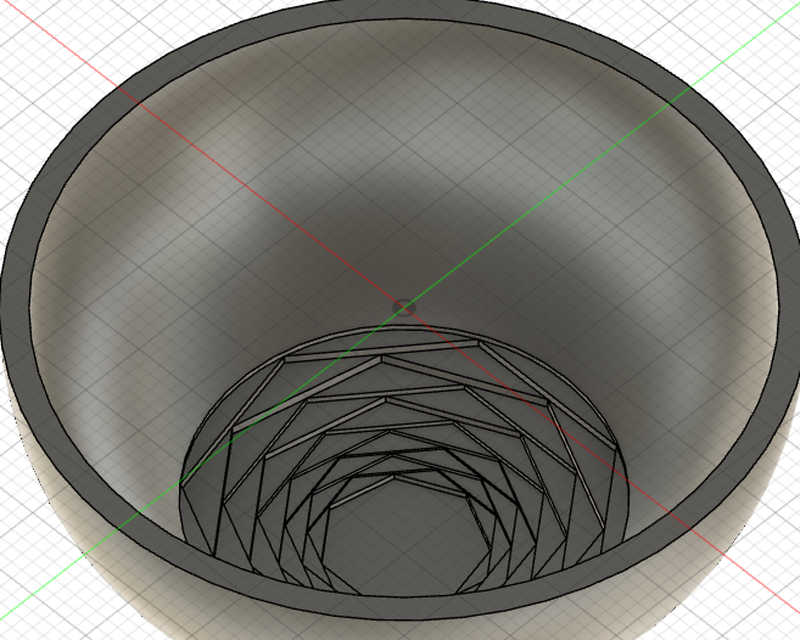
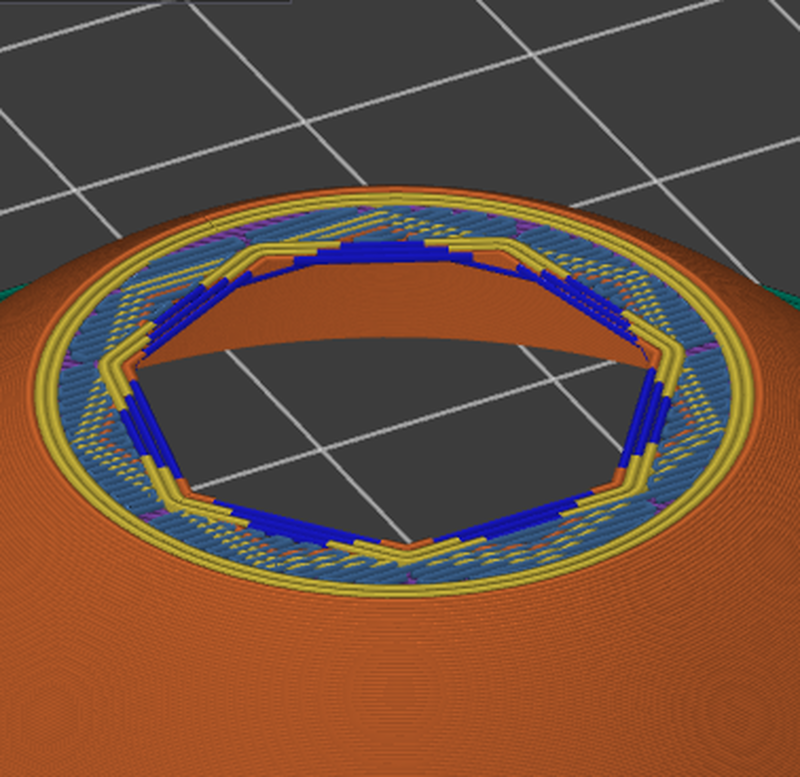
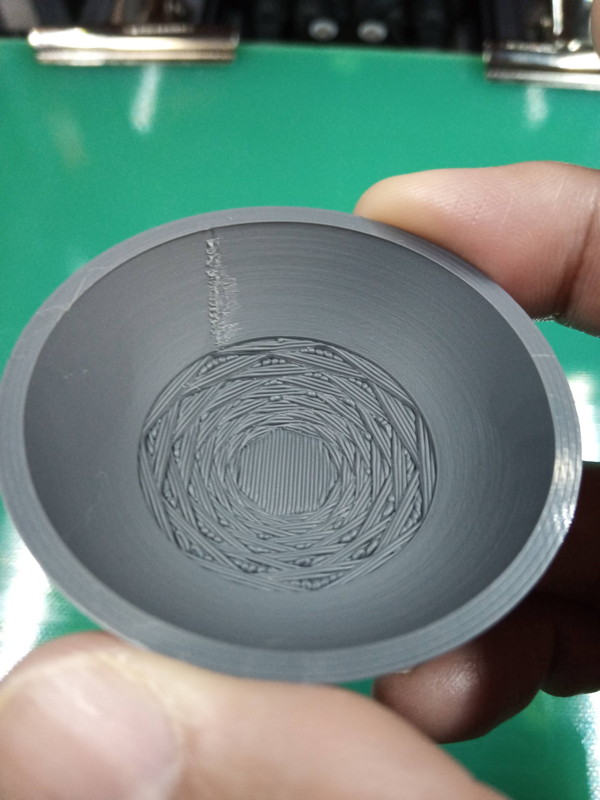
Prusaslicerでのスライス結果を見ていただくとわかりますが、内側を多角形が覆うことでノズルのパスも直線になります。接線方向のブリッジを組み合わせてオーバーハングを克服するモデリングテクニックです。出来上がりの裏面もとてもキレイで、近似的な形ではありますが意匠も良いと思っています。(ひと手間かかりますが)
最近、ネジ穴部分等、ザグリと呼ばれる加工をする際にはつい先日Fusion360用のプラグインが発表されており、moyashiさんが教えてくれました。
この線、何かというとここに小さな段差が作られています。見えている面が底面側に来た際、中心の小さい穴周囲の壁をいきなり作ることはできないので、サポートが必要になります。このアドインを利用することで、円の接線部分で樹脂を橋渡しして平面を作り、最後に中心に円を描くことができます。
上の球形では自分で7角形を作っていましたが単純なザグリ穴ならこのアドインを使うとパパっと加工ができるので非常に便利だと思います。
詳細はツイートからGithubの当該ページへどうぞぜひどうぞ!
自分には上のような球面を作るアドインを作れませんが、良かったらどなかか作成をお願いいたします・・・
スライサー設定 積層は薄めに 可変積層も有効活用を
モデリングの工夫で補えないところや意匠の問題でオーバーハングを作らざるを得ない場合はどうするか、そこで次の工夫がスライサーです。基本的な設定としては下記になります。
- 造形方向を工夫する
- 積層厚を薄くする
- 下に凸の場合はサポートを広めにしっかりつける
積層強度のこともあるので一概には言えないのですが、許される範囲でオーバーハングが少なくなるように造形方向を調整する必要があります。造形物をきれいに作ることとサポート量を減らすこと、オーバーハングを少なくすることの両立は結構難しいと思います。
また、積層は薄いほうがオーバーハングには有利です。空中に直接樹脂を置くことはできないので、一つ下の層との水平距離(重なり)が大事になりますよね。積層が薄ければきつめのオーバーハングでも距離が相対的に少なくなるため失敗のリスクが減ります。ここは、次のPrusaslicer 2.6の新機能と密接に関連しています。
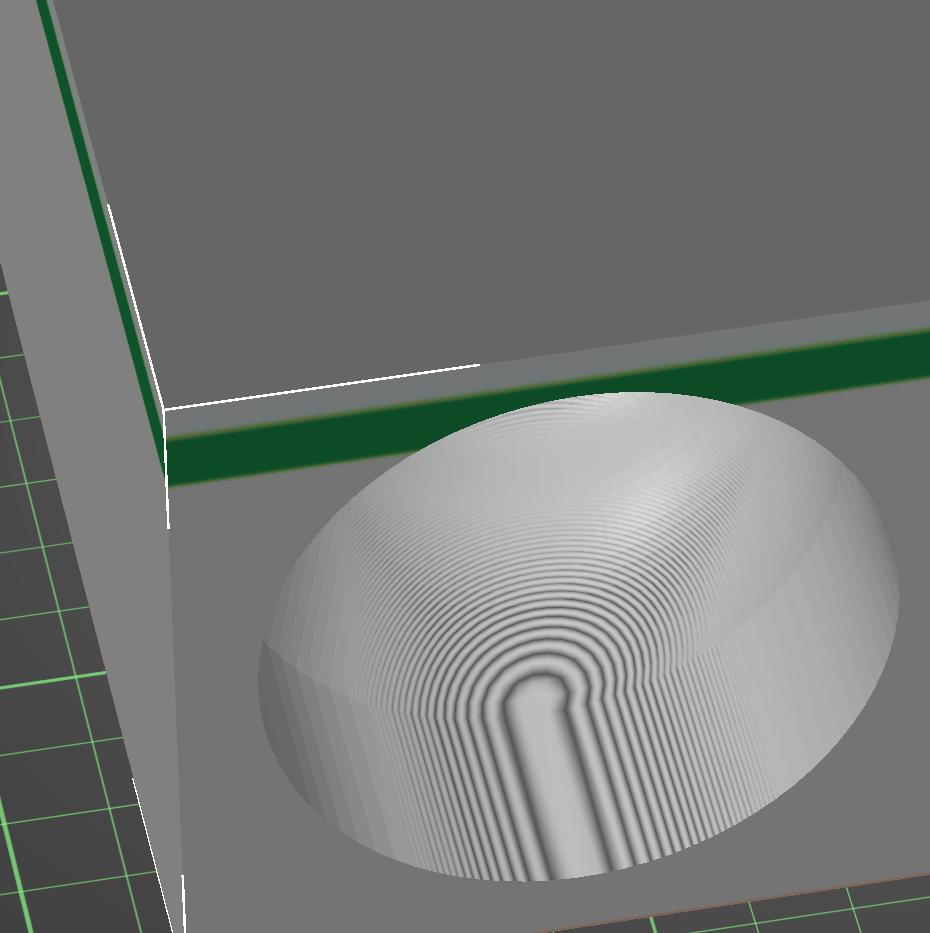
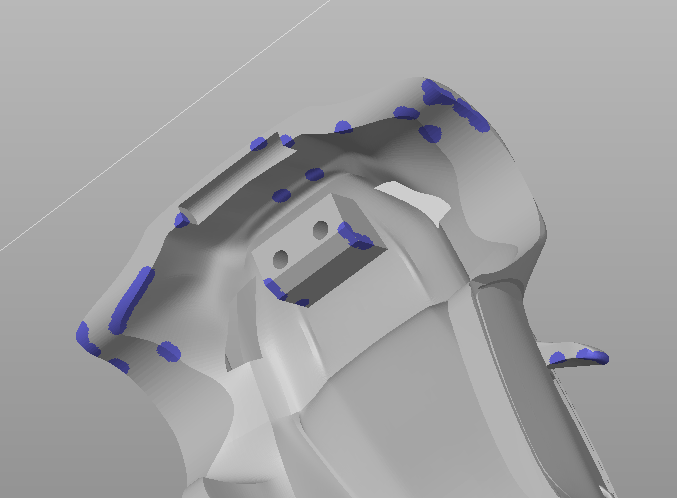
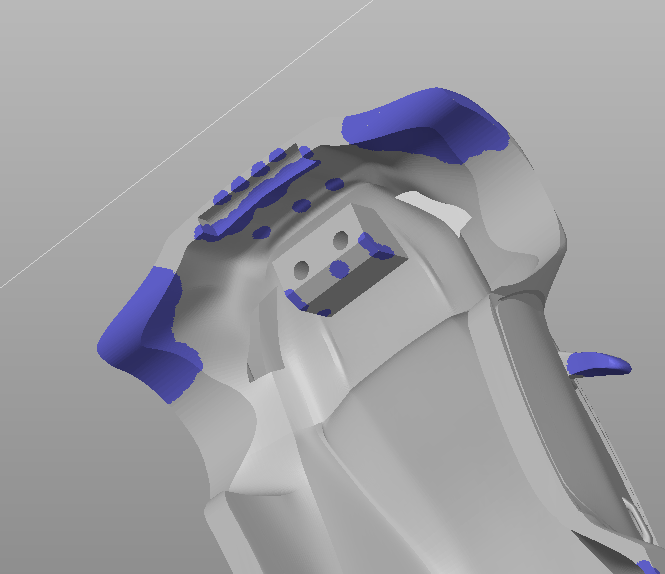
全部の積層を薄くすると造形時間がかなり増えるので、可変積層機能を利用してオーバーハングがきついところだけ積層を薄くするのがいいと思います。
また、形状としてサポートが必須な下に凸な部分はその周囲のサポートをしっかりつけることでぽろっと取れてしまうのを防ぐことができます。こういった形状が多い場合はサポートとのz方向の距離を離しすぎないのがコツだと思います。
Prusaslicer 2.6の最新機能 Dynamic overhang speed と Extra perimeters on overhangs
さて、最新のPrusaslicer 2.6(α3版で確認)ではオーバーハング関係で大きなアップデートが2つあります。それが見出しの「Dynamic overhang speed」 と 「Extra perimeters on overhangs」です。
まずDynamic overhang speedですが、これはオーバーハングがきついとき、その下の層との重なり具合に応じて造形速度を遅くする機能です。オーバーハングでの重なりが少ないのに造形スピードが速いと積層の密着が得られず、樹脂がパスをショートカットして浮いてしまうことがあります。それを防ぐためにオーバーハングの時だけ造形スピードを下げるのがこの機能です。オーバーハングをゆっくりに前層することで前層と密着し、また樹脂を十分冷却することができます。おそらくファンのフローはなるべく上げたほうが効果的だと思います。

Extra perimeters on overhangsは個人的にかなり嬉しい機能です。これはオーバーハングがきついときに外壁のパスを変化させてオーバーハング耐性を上昇させます。具体例は公式サイトにもありますが、既存の壁から少しずつ伸ばすようにパスを描くことでオーバーハングが崩れにくいようにしています。下の写真が私が試したものです。積層は0.1mmと0.2mm。本バージョンで使用できるテキストのエンボスやカットツールを使用して造形しました。オブジェクト毎に造形設定を変えられるとこういう比較がしやすくて良いですね・・・!造形に直接書き込んであると後から見返す時も便利でした。
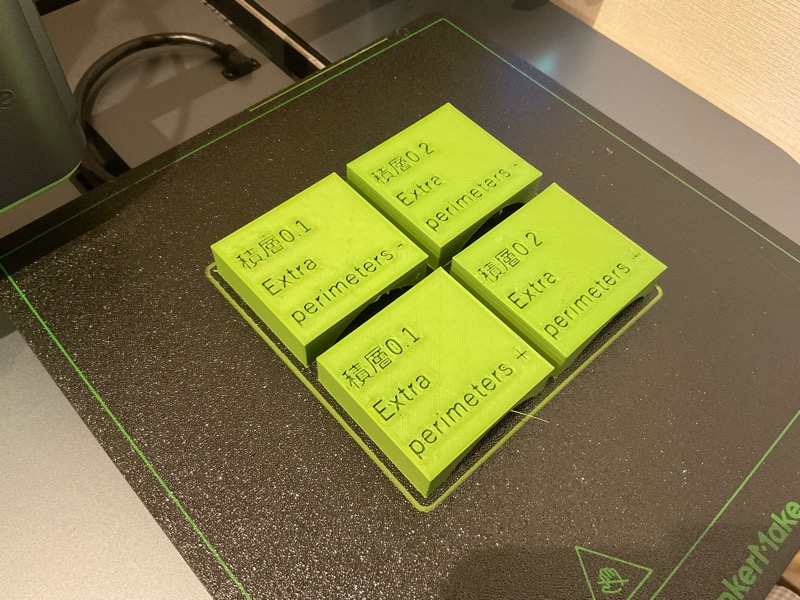

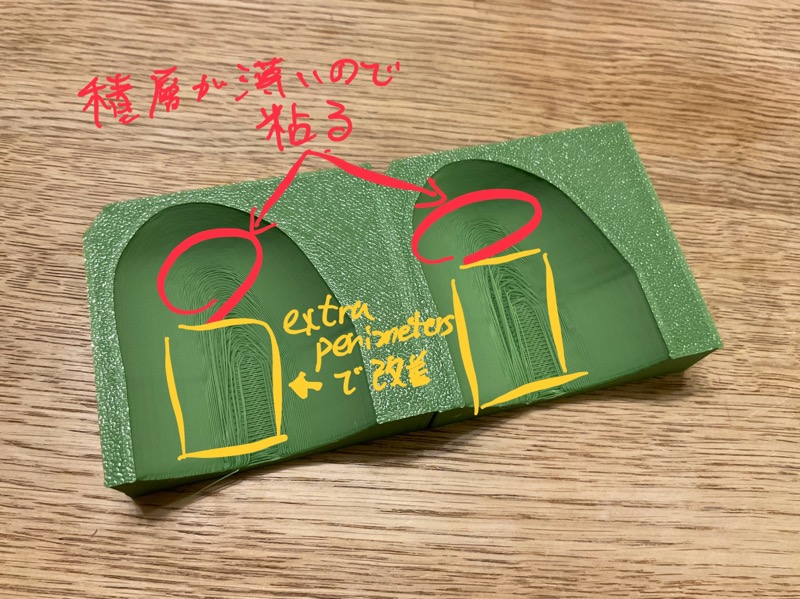
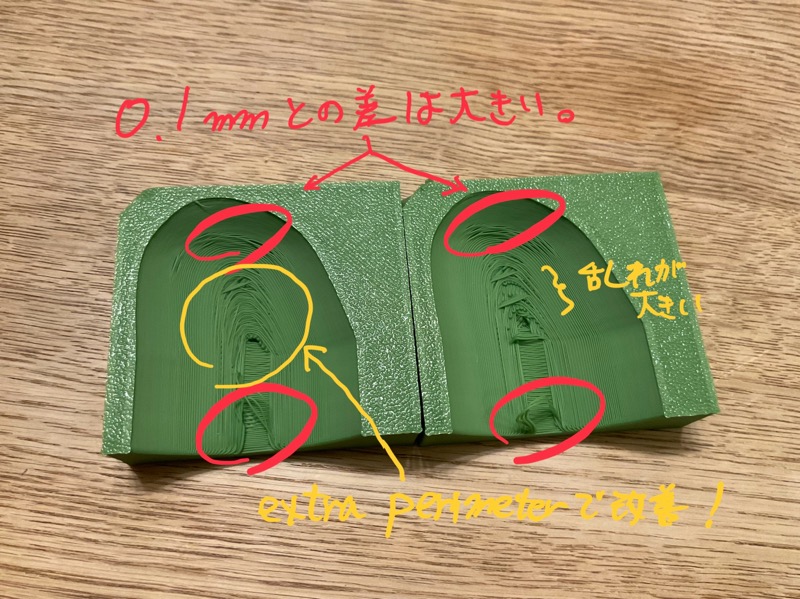
せっかくなので比較的大きな筒状のSTLをカットツールで切り出し、エンボス加工で積層設定を埋め込み、それぞれ条件を変えて造形しました。向かって左が0.1mm積層、右が0.2mm積層です。やはり積層は薄いほうが結果が良く、またextra perimetersを有効にしたほうが乱れが少なくなっています。このシビアなオーバーハングがしっかり造形できるのはさすがの0.1mm積層です。0.2mmと比較して全体的にきれいにできています。以下に3MFファイルもおいておきますのでよかったらご自身の環境でお試しください。
Prusaslicer2.6以降をお持ちであればこの3MFファイルを使って上記の確認ができると思います。パスの確認等にも使えると思いますのでご利用ください。
厳しいオーバーハングの造形時にはスライサーのパスを確認しよう
こういった造形が厳しいと予測される場合にはスライサーでパスをしっかり見ておくのが肝要です。造形を開始する前に失敗の可能性に気付けるとよいですよね。上のファイルのスライスはこんな感じです。
0.1mm積層のほうがオーバーハングを細かく刻んでスライスしているのと、Extra perimetersをオンにしたほうが補助の壁が出来ていることが確認ができます。(適宜停止してご覧ください)必要に応じてそれぞれのパスの詳細を確認し、オーバーハングが克服できているか確認してから造形したほうがベターです。
今回も最後までお読みいただきありがとうございました!どなたかのお役に立てば幸いです。今後ともよろしくお願いいたします。
ディスカッション
コメント一覧
まだ、コメントがありません